What colour is your parachute?
MadeForOne.com profiles parachute manufacturer Performance Designs
2004-05-28: The title above was originally used on one of the many 'self-help' books that are published every year, but in the case of Peformance Designs, the question can be asked in a more literal sense. This DeLand, Florida, USA based company will build a parachute with a customer's personal colour scheme.
Performance Designs was founded in 1983 by Bill Coe. The following year, he enlisted the help of John LeBlanc, formerly a fellow student of Bill at Embry-Riddle Aeronautical University. Since then, they have been at the forefront of parachute design innovation.
Innovative design of the company's early canopies catapulted Performance Designs to the lead position in 'ram air' parachute design. One of the earliest areas of innovation at led to research in the area of low drag suspension line, resulting in the development and use of 'microline'. Made out of Spectra fibers, microline cut suspension line drag in half, increasing performance dramatically. Microline has gone on to become an industry standard. Throughout the 1980's and 1990's, Performance Designs continued to develop new designs in main and reserve canopies.
Around this time the limitations of existing materials used in parachute construction were becoming more apparent. Performance Designs responded by devising a process to produce a completely zero porosity fabric. This process was provided to a fabric converter, modified, and finally manufactured in production quantities. In 1989, after four years in development, the Sabre model was born, utilizing the capabilities of the zero porosity material. This canopy model remains in production to this day.
In addition to developing parachute designs, Performance Designs has also worked to develop new manufacturing methods. In pursuit of not only efficiency, but also consistency, Bill Coe designed and constructed a computer-controlled, laser cutting system for cutting parachute material. Kevin Schafer, Marketing Manager of Performance Designs explains: "We currently have 2 laser tables on line and a 3rd being built. They are about 100 feet in length each. The laser tables purpose is to cut all the various pieces that make up a parachute. These laser tables were designed, developed and built in-house - Bill Coe, the owner of the company, conceived the idea and made it happen. All parts are sourced and the tables constructed in the facility. This is a reason that other manufacturers do not use this technology - it is not commercially available. You cannot buy a laser table to cut parachute fabric, you have to build it yourself." It is believed that no other parachute manufacturer in the world uses laser technology to cut parachute fabric.
Performance Designs laser table Picture: Performance Designs, Inc.
The actual parachute construction is started when laser operators will lay out the fabric on the table, then program what pieces are to be cut. Once the laser has done its job, they go around and collect the pieces off the table. After the wasted pieces are removed, they start again by laying out another piece of fabric. The laser tables have made it possible to trace each and every piece of material through a laser cut code, increasing the consistency of canopy manufacturing.
Every parachute is sewn together by seamstress operators - nothing in the production is automated except the actual fabric cut out. Performance Designs has five different inspection areas, meaning many eyes run over a parachute before it reaches the customer.
Today, Performance Designs markets eleven models of sport parachutes, plus accessories. There are also two separate models in powered parachutes and select range of military specification canopies. For the purpose of this article, we will concentrate on the sport models. Each product has its own distinct characteristics. For those of us who are unfamiliar with the sport of skydiving, we might think that all parachutes behave in a similar manner - they open, and the drag of air on the canopy slows the skydiver's descent to earth. However, things are far more complex than this. The variation in canopy design can influence the smoothness of opening, speed of descent, manouverability, even the type of "swoop" on landing.
For anyone looking to understand skydiving theory, the Performance Designs website contains a comprehensive section on education and canopy selection. Two important terms are 'Exit Weight' and 'Wing loading'. Exit weight is the skydiver's body weight, plus the weight of clothing, rig, both canopies, and anything else worn when exiting the plane. Wing loading is the relationship between the skydivers exit weight and the canopy's surface area. A higher wing loading increases the speed of a canopy.
Some of Performance Designs current sport models include the most recent version of the Sabre, the Sabre 2, which provides consistent, soft, on-heading openings and maintains strong ease of landing and forgiveness at lower wing loadings. The Navigator is specifically designed to address the student's need to learn canopy piloting skills. It is the first canopy to bridge the gap. With its agile, crisp handling at student wing loadings and corresponding lower (student) airspeeds it gives the student what they need.
Stiletto is the canopy of choice for those pilots who have taken the time (and jumps) to hone their piloting skill. It has been the canopy flown by more national and world champions than any other canopy in the world. At the top-end of the range are the Velocity and Vengeance for experienced skydivers. The Velocity is designed specifically to satisfy those pilots who have already been jumping high performance elliptical canopies at relatively high wing loadings, for some time, and are looking for something more. With this model, it is easy for an experienced pilot to achieve incredibly steep, high speed turns. It also allows long, high speed swoop landings, while still allowing the skydiver to slow down more than with any other canopy of a given size.
The Vengeance canopy is the result of over two years of constant research and development. The Vengeance is said to offer the next level of flight and landing performance, coupled with the benefits of the patented 'airlock' system. This gives soft openings as well as " unsurpassed responsiveness, and incredible speed range". It has been designed to allow the pilot to build up higher speeds, if desired, for swoop landings. Performance Designs say that, regardless of the approach technique used, this canopy generates more lift at low speed (touchdown) than any non-cross braced canopy ever built.
So where does the customisation come in? On Performance Designs website (www.performancedesigns.com), there is an online store, where customers are first asked to nominate a local reseller through which the transaction will be completed. There are dealers in most parts of the U.S. and many other countries around the world. A customer can purchase a standard design of parachute from stock, but there is also a custom design option.
With something as life-critical as a parachute, you would not expect a supplier to provide customers with the option of 'experimenting' with their own designs. However, a customer can stamp their personal touch by designing the canopy colour scheme, using Performance Designs' online painting tool. This is a Macromedia Shockwave plug-in which runs within the ordering webpage. Designed to resemble a painting program, customers can select various colours from a palette of 19 colours, and 'fill' each section of the canopy to produce their chosen colour scheme. Depending on the design of canopy, there may be a few dozen individual sections, providing plenty of scope for individualisation. Perhaps because they make parachutes and are always thinking of reserves and backups, Performance Designs also provide two more basic product configuration facilities. The first is a webpage page for users who do not have Shockwave installed, where the sections are matched to colours on drop-down lists. The second is a downloadable form which can be filled in and faxed to the local agent.
In addition to the colour scheme design, the customer can also select the canopy size and type of fittings from drop-down lists. For example, the Katana model comes in 5 sizes - 83, 89, 97, 107 and 120 - these are all square feet, e.g. 83 square feet. MadeForOne.com tried out the facility using the shockwave plugin, and it certainly gives a great deal of scope for personalisation of the canopy colour scheme. There is a a selection 19 colours to choose from.
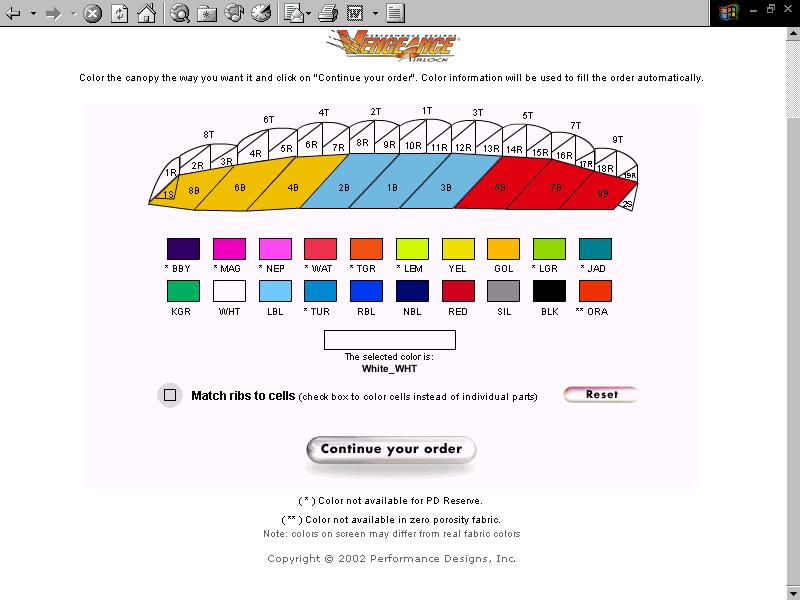 The Performance Designs parachute design page, showing some canopy sections filled using the MadeForOne logo colours
The lead time for a custom designed parachute is around ten weeks. While the skydiver is waiting for the new personalized parachute to arrive at the local dealer, he or she can take comfort in the fact that the custom design will cost the exact same as an equivilent off-the-shelf example. Once someone is out of the plane and falling, however, it is likely that more pressing concerns occupy the mind.
|