Will 'Fabbing' Turn the Industrial Revolution on its Head?
The revolution in commerce brought about by the Internet since the mid-1990's has been a major factor in the advancement of mass customisation. A product can be configured quickly on a mass customiser's website and the order can then be checked and confirmed. Of course, the finished product cannot be transmitted back to the customer through the telephone line. A three-dimensional object has to be forwarded by post or other delivery channel. Or does it? The science to create three-diminsional objects directly from computer data already exists, and is used by enterprises in 'Rapid Prototyping' of new designs. Welcome to the world of Digital Fabrication, or Fabbing.
We are all familiar with the way a computer printer lays down ink on a page, creating a two-dimensional image or lines of text. The concept of fabbing (also called Digital Manufacturing) is similar, but instead of printing text or images, data is taken from a Computer Aided Design (CAD) file to create a three-dimensional object, by building up layers of material to form the required shape. The machine used to create this object is called a Digital Fabricator, or 'Fabber'. A digital fabricator is a device that makes things automatically from computer data and raw material.
The data format used in fabbing is StL. An StL (StereoLithography) file is a triangular representation of a 3-dimensional surface geometry. The surface is tessellated or broken down logically into a series of small triangles (facets). Each facet is described by a perpendicular direction and three points representing the vertices (corners) of the triangle. These data are used by a slicing algorithm to determine the cross sections of the 3-dimensional shape to be built by the fabber.
What If?
At this point in time, the state of development and cost of digital fabricators is not yet at a point that will trigger widespread consumer use. However, as with photocopiers and laser printers, the use of fabbers will become more common as the technology is developed and the costs are reduced.
If fabbing technology were to be developed to the stage where it became accessible to consumers or small business, it could have an impact on the World equal to the invention of the printing press or the internet. Take this example:
Imagine for a moment that you want to buy a garden chair. You can go out and buy one at a garden centre. That takes time. You have to get to the shop. If you are driving, you have to park your car. You may have to queue at the checkout. The internet provides an alternative - you can find an online garden store and order your chair online. However, while you can stay at home, it will be at least a day before your chair arrives. If you had your own fabber, you could log on to an online garden furniture data store and buy a chair CAD file. You could then download the file to your fabber, which would 'create' the chair directly from the data. If the technology of fabbers can be developed to handle more than one component material, the same principle could be applied to any other three-dimensional object.
Now, imagine that the cost of a fabber falls within reach of most households. Why would people want to go out and buy things, when they could buy them on the net and have them literally appear out of a machine in their home? From the point of view of the garden furniture company, why should they order 100,000 chairs from a sub-contractor when they could just as easily sell a StL file to consumers who could produce it themselves? In theory, what we are talking about here is the end of centralised manufacturing. Hence the question "Will fabbing will turn the industrial revolution on its head?" After all, the industrial revolution brought manufacturing away from the home or the small workshop, and into large industrial facilities. Fabbing could do the reverse, by allowing companies to sell data that can be turned into three dimensional objects at home.
The more likely situation is that digital fabrication would become established alongside conventional delivery methods. People would still visit shops and order goods online for delivery by mail. However, just as the internet has revolutionised the ordering of purchases, digital fabrication could do the same with delivery. The digital fabrication method may yet become the chosen delivery channel for a significant percentage of all purchased consumer and industrial products.
It is possible that future homes would have a 'fabbing room', where consumers would shop for durable goods and have them fabricated on-the-spot. Theoretically, the raw materials could stored in a garage or basement and be fed through a network of pipes to the digital fabricator in the fabbing room.
The Impact on Economies
If fabbing becomes widely used, it has far-reaching implications for both developed and developing countries. It could mean a significant fall in demand for manufacturing labour, as manufacturing companies become 3D data companies. The potential reduction in demand for low-skill labour in particular could result in large scale social unrest in many countries. For established brand name consumer goods companies, the prospect of reducing their reliance on manufacturing might be an attractive one. Many of these enterprises are now design and marketing companies, for whom manufacturing is simply a bought-in service, often outsourced to low-wage economies. Were fabbing to become commonplace, the profitability of large corporations could increase dramatically. Why? If we look at present day enterprises who sell data products (for example, a training manual) over the internet, the incremental cost of each sale is effectively zero. In other words, once the manual has been written, edited and placed on the server, there is no additional cost when each new customer downloads a copy. By contrast, consumer goods enterprises must currently pay for the materials, labour and shipping for every additional item sold. If these companies could become sellers of 3D data, their incremental costs would fall to zero, and they could still use the value of their brand to maximise profitability.
The result of this would be a flow of wealth towards those countries with the highest number of established brand names. However, it would subsequently also allow new brands from developing countries to become established more easily, since a greater share of the overall investment amount could be put into building brand awareness. The probability remains that these new brands could still compete strongly on price, since the discrepancy in costs between developed and developing countries would continue to exist for designers and marketers in the same way as for manufacturing staff.
Types of Fabbing
There are a number of different techniques that can be used for Digital Manufacturing. Subtractive methods, such as carving or milling, involves starting with a solid block, and removing material a piece at a time to form the desired shape. These have been in common use for many years. The approach currently used in rapid prototyping is Flat-layer additive fabrication. Amorphous material in the form of a liquid, powder, or adhesive film is caused to build up in flat layers in the proper sequence of shapes to make up the desired shape. This can be done by Stereolithography - adding one slice on top of another in a vessel of liquid polymer, or Selective Surface Curing, where successive layers of a liquid resin are cured by a scanning laser or masked lamp working at the top or bottom surface of the resin.
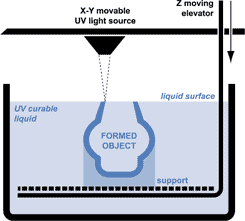 StereoLithography diagram. Image: Materialise NV
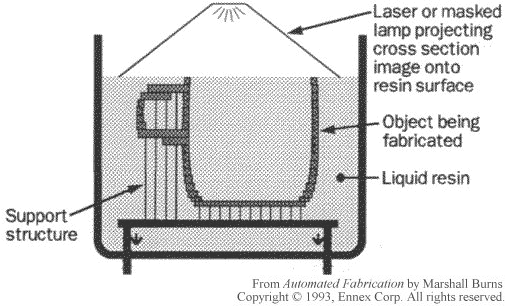 Selective Surface Curing diagram. Image: Ennex Corporation - Used with permission.
Other methods include Selective Sintering, where a powder is caused to melt in specific locations, and the melted powder then fuses into a contiguous solid, which builds up the shape of the desired object. Heat is currently supplied by a laser.
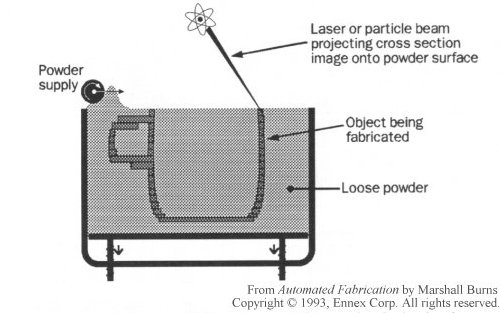 Selective Sintering process. Image: Ennex Corporation. - Used with permission.
Deposition, which involves depositing successive layers of a fusible material. This may be done by laying a continuous stream of material (continuous deposition), by jetting a stream of fusible droplets (drop-on-drop deposition), or by jetting a stream of binding droplets on successive layers of a powder (drop-on-powder deposition).
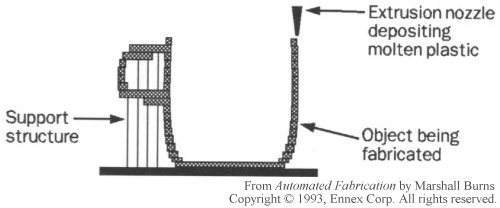 Continuous deposition process. Image: Ennex Corporation - Used with permission.
A recent MadeForOne.com article described how Belgium-based company Materialise NV uses stereolithography and sintering, both in rapid prototyping for industry, and also to produce designer lighting products for the consumer market.
More advanced methods that could be used in the future include alternative curing or sintering techniques, such as by electron beam instead of by laser, or by a panel of light-emitting diodes (LEDs), an array of microlasers, or a digital micromirror device (DMD).
Alternative deposition techniques could also be used, such as depositing a stream of powder into the path of a scanning laser, inducing vapor deposition by a scanning laser, or depositing a pattern of two complementary powders in which one is and the other is not subject to fusing by a postprocess such as melting.
A further development is Edge-controlled layer-additive fabrication. This is a modification of some of today’s flat-layer techniques in which a particular slope or curvature is induced in the edges of the layers. This eliminates or reduces the "stair step" effect which causes a rough surface on sloped edges of objects made by layer-additive techniques. It also allows for much faster fabrication by allowing thicker layers to be used.
Future fabricators will go beyond the limitations of just subtractive and flat-layer additive techniques. One idea which is being explored is Curved-layer pattern lamination, in which the succession of adhesive patterns is laid up on a curved-surface base. Another concept is Freeform fabrication, in which the product is built up additively in arbitrary fashion, not constrained to a sequence of flat or curved layers.
The Digital Fabricator Market
At this point in time, the cost of Digital Fabricators is delaying their widespread adoption. However, as with photocopiers and laser printers, the use of fabbers will become more common as the costs reduce. One of the longest established suppliers is 3D Systems of Valencia, California. This company was founded in 1986 and has a variety of products suitable for different types of digital fabrication. They have developed an office-friendly fabber called the Envision, which costs in the region of $30,000. Others include Stratasys of Eden Prarie, Minnesota. Stratasys has developed an office based fabricator called the Prodigy Plus system. This product allows designers to make durable ABS models with moving parts. Another Stratasys fabricator, the Maxum, was used to create the child's trike shown below. The ABS plastic parts were sanded and painted to produce a realistic functional model.
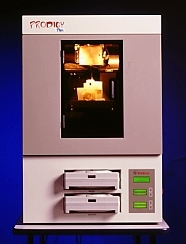 The Prodigy Plus from Stratasys. Image: Stratasys
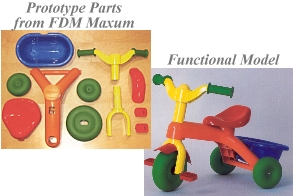 Trike prototype made using Stratasys Maxum fabricator. Image: Stratasys
Another company which has made inroads into smaller-scale digital fabricators is Solidscsape Inc. of Merrimack, New Hampshire, whose Model Maker Desktop 3D Modeling System is used in the jewellery industry. The T66 can translate CAD designs from most jewelery and engineering design software into 3D casting patterns. It is used to fabricate objects up to 15.24 cm in height, width and depth. A larger model, the T612, will create items of similar height and depth, but allows 30.48cm width.
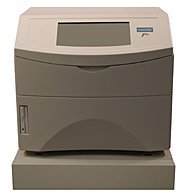 Solidscape's T66 fabricator Image: Solidscape Inc.
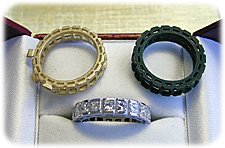 Examples of jewelery castings made using the Solidscape T66 Image: Solidscape Inc.
Obstacles to Widespread Fabber Adoption
Apart from cost issues, there are a number of factors which would delay the development of digital fabricators for home use. The first of these is the level of technical knowledge required by consumers. While CAD applications are becoming more user-friendly as time goes on, there is still a significant level of technical knowledge required to operate one. Perhaps an opening exists for a browser-style application with the specific purpose of processing downloaded StL files to a fabber.
A second very important issue is the intellectual property question. Digital fabrication is sometimes referred to as 'Napster Fabbing', after the controversial Napster file-sharing programme, which allowed consumers to share music files without paying any royalties to the publishers. Unless safeguards were built in to StL data, there would be nothing to stop one person purchasing a file and then sharing it with others who could then each fabricate their own product, without paying anything to the original vendor. The obvious solution is to build some form of protection into the data, so that it could only be used by one customer, but as with any protective data device, there remains a risk that it could be hacked. A second option would be to send the purchased StL file as a stream of data directly to the fabricator, rather than to the customer's PC. If the fabricator were to have an Internet Protocol (IP) address of its own, it should be possible to do this. This option would probably require a home network to be set up, rather than just connecting a fabricator to the PC with a USB cable.
To date, additive digital fabricators have generally worked with one material only, usually plastics. Many products are made up of multiple materials, adding to the complexity of fabrication. Also, many products have in-built mechanisms to control functions, which are difficult to replicate using fabbing techniques.
Digital Fabrication - The Opportunities for Mass Customisation
Digital Fabrication presents opportunities to mass customising enterprises to look at their product range in a new way. Instead of viewing themselves as making products to order, they could become service enterprises. This would require a change of approach to prodcut configuration. Instead of taking a customers desired configuration and turning it into a product within a day, the 'fabbing configurator' would have to take the configuration data and adjust the StL data accordingly within a few seconds, and then allow the customer to download the file.
It will be interesting to see if the potential of digital fabrication will be realised in the near future. Things might never be the same again.
Editor's Note: My thanks to Marshall Burns, Phd of Ennex Corporation for his assistance in the completion of this article.
|